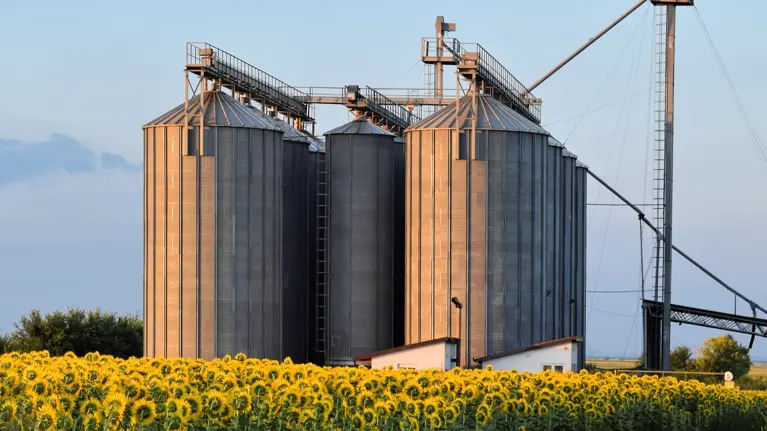
Delta Wilmar: Holistic Business Transformation with SAP S/4HANA ERP
Migration to SAP S/4HANA helps a leading agro-industrial company streamline business efficiency
Business Challenge
Implementation of the new advanced IT technologies lays at the core of Delta Wilmar IT strategy. Functionality gaps as well as weak integration of SAP ERP with the legacy 1ะก systems, previously used at Delta Wilmar, called for quick changes:
- Absence of end-to-end automated control over business processes lowered operational effectiveness, leading to processes fragmentation and lack of transparency.
- Immaturity of legacy systems was hindering business growth.
- Inconsistency of information from isolated sources affected decision-making processes.
- End-to-end business scenarios had numerous grey areas. Their optimization was impossible without additional analysis to understand the essence of the ongoing processes.
Delta Wilmar wanted to implement an integrated platform that would provide complete, timely and accurate business-critical data to company management for further in-depth analysis, assessment of the enterprise activities and decision-making procedures. Along with better data analytics capabilities, our client wanted to update their enterprise management system, improve data integrity, reliability, and consistency, and reduce TCO for business applications support. All this would be possible with the transition to SAP S/4HANA platform.
Since the transition would affect and shape numerous business processes, the functional scope of the future system comprised a number of SAP modules, which had to be implemented within the scope of the transformation project:
- SAP DMS for coordination, management, and control of contract execution
- SAP FI/FM/CO for financial processes: accounting, fixed asset accounting, cost analysis and controlling according to local and international laws
- SAP MM/SD/LE-TR for improvement of logistic processes: management of procurement, stocks, sales processes and processes of transport logistics (railway, motor transport, shipping)
- SAP PP/QM for production planning and quality control processes, etc.
Delta Wilmar selected Tietoevry Create Ukraine (formerly Infopulse) as a core implementation partner based on the availability of the necessary SAP expertise, an all-round understanding of all requirements of this complex project, as well as company reliability and financial stability.
Solution
We started the SAP S/4HANA transformation project in November 2017. It took almost 14 months from initial requirements analysis to system deployment, and an extra 3.5 months for post-migration support after going live.
Since the transition affected and shaped numerous business processes, the functional scope of the future system comprised a number of SAP modules, which were implemented within the scope of the transformation project:
- SAP DMS for coordination, management, and control of contract execution
- SAP FI/FM/CO for financial processes: accounting, fixed asset accounting, cost analysis and controlling according to local and international laws
- SAP MM/SD/LE-TR for improvement of logistic processes: management of procurement, stocks, sales processes and processes of transport logistics (railway, motor transport, shipping)
- SAP PP/QM for production planning and quality control processes, etc.
Migration to SAP S/4HANA platform was conducted in accordance with the SAP Activate framework:
- Prepare. Based on the results of the initial preparations (2 months), we created a project roadmap, formed a project team and deployed a prototype of SAP S/4HANA solution.
- Explore. In the second stage of the project (4 months), we carried out a FIT-GAP analysis of standard SAP best practices, described target business processes, and created a backlog.
- Realize. During the third stage (5 months), we conducted the necessary system tuning and developed missing functions. Upon running a number of test cycles with SAP CBTA, including the final integration testing of the end-to-end business scenarios, the solution was ready for deployment. In parallel, we developed interactive end-user video instructions with SAP Enable Now.
- Deploy. During the deployment stage (3 months), the production environment was prepared, which allowed migrating the data to the new system. At the same time, our specialists conducted training of key users and ensured organizational readiness. On Jan. 1, 2019, the new SAP S/4HANA system was put into operation.
- Support. Finally, for the next 3.5 months, we provided support and maintenance of the productive operation of the system.
Together with Delta Wilmar, we worked closely to develop approximately 300 custom functionalities for the SAP S/4HANA platform. While the system at its core relies on standard modules, we delivered a great deal of custom business-critical components.
After the successful rollout and 3.5 months stabilization period, we continued to support Delta Wilmar, helping to resolve issues and developing additional functionalities.
Technologies & Tools
- SAP S/4HANA
- Modules: FI, CO, FM, MM, LE-TR, SD, PP, QM, DMS
- SAP CBTA
- SAP Solution Manager
- SAP Enable Now
- SAP Activate Methodology
Business Value
Delta Wilmar Group received a unified SAP S/4HANA platform that provides a full range of tools for effective management of their business for 300+ users. The integrated system allowed to migrate from legacy systems, standardize master data, and significantly increased the overall effectiveness and accuracy of the company business processes while supporting their rapid re-engineering. This transition enables Delta Wilmar to quickly adapt to the ever-changing conditions of the local and international agricultural markets. While the functional scope of the project provided numerous integrations with both internal and external systems, SAP S/4HANA platform has become a basis for the further development and improvement of the corporate business processes.
The following KPIs were achieved in the course of the project:
- FI/CO – Finance and Controlling: automated and improved the effectiveness of controls in credit management.
- MM – Purchasing: better traceability and control of the entire supply chain, as well as the quick adaptation of the system to business changes.
- LE – Logistics: transparent quantitative and qualitative accounting, control at all stages of product acceptance and shipment.
- SD – Sales: reduced the risk of fraudulent transactions, improved traceability and control of the entire sales chain.
- PP – Production: better traceability and control of oil and fat balance, harmonized and standardized Master Data, improved automation of material requirements planning, more accurate production planning.
- QM – Quality Control: ensured quantitative and qualitative accounting of products at all stages – from purchase, transportation, and storage of raw materials to production, storage and sale of finished products.
- SAP Enable Now: continuous transfer of knowledge from our consultants to Delta Wilmar project team, as well as key DW Team users training.
Close collaboration with the client, as well as direct involvement of the company owners, greatly contributed to the success of the implementation of the solution. This project has laid the foundation for the business transformation of the entire Wilmar International Holding with the subsequent implementation of the SAP S/4HANA platform, in this way increasing the importance of this migration success.
As the next step, we planned to expand the functionality of the system and implement other modules, including SAP EWM for warehouse management and SAP PM for repair management.
Focused on strategic growth and operational sustainability, Delta Wilmar strives to build its business processes on the basis of the most advanced and effective technologies. With the global transition to the SAP S/4HANA platform, we aimed to improve the internal efficiency of the company, achieve better integrity of functions, automation of processes, and unification of workflow with balanced TCO. Upon analyzing implementation partners for this business transformation project, we made our choice in favor of Infopulse (now known as Tietoevry Create Ukraine). As practice has shown, it was the right decision. In the course of the SAP implementation project, they have repeatedly confirmed the status of a reliable partner. They have proven expertise with an all-round understanding and excellent execution of all requirements of this complex project.
- Olga Rybachuk, Chief Financial Officer at Delta Wilmar, Project Sponsor
Technical Details
The SAP S/4HANA solution supplied to Delta Wilmar enabled the following functions:
FI — Finance
- Data entries without duplications
- Increased efficiency of operations:
- Intercompany operations automation
- Processing automation: bank statements processing, tax invoice generation, calculation of exchange rate differences
- Parallel IFRS accounting in two currencies — UAH and USD
- Implemented Agile/Scrum approaches as well as set up DevOps processes to speed up delivery.
FM — Funds Management
- Automated volume control of budget availability for all relevant operations
- Liquidity planning reporting
CO — Controlling
- Implemented a unified controlling methodology
- Integration of cost accounting with financial and material accounting
- Management reporting for the cost of production processes and product costs analysis, profitability analysis by business areas/market segments
- A deeper understanding of costing calculations for further analysis
DMS — Document Management System (Contracts Management)
- Total control over the execution of the contract: operations will be blocked if they don’t comply with contract conditions
- Acceleration of contract preparation, using templates to form the contracts (79 templates)
- Electronic reconciliation of contracts and business partners
- Documents security storage and traceability (audit trail)
MM — Material Management
- Transparency and acceleration of procurement operations:
- The intercompany process ensures documents auto-generation for related company codes (mirror docs forming)
- SF crush tolling process ensures documents auto-generation for related company codes (mirror docs forming)
- All material operations in a single ERP system (instead of 3 different systems that were used before)
- Material accounting by batches for traceability analysis
- Real-time radars/flowmeters integration with auto-postings to SAP (SCADA-SAP integration)
- On-line terminal stocks control with required analytics level (by tanks)
- Master data management: obsolete and duplicate data were cleared; data enrichment was done (additional analytics)
- MRP automatically ensures that only the required materials will be ordered
LE — Logistic Execution
- Total control over the logistic processes execution: trucks/wagon operations block if check criteria were not met (quality, quantity, contract conditions, etc.)
- Real-time weighbridge integration with auto-postings to SAP
- Real-time railway integration (Ukrzaliznytsia client)
- Correct freight costs calculation & allocation
SD — Sales and Distribution
- Total control and transparency of Sales processes execution:
- Credit Management — limit exceeding blocks for any further contract operations
- Control of contract conditions and terms on each step of sales processes
- Online stock balance and shipments monitoring
- Increased efficiency of daily operations:
- Processing automation: pricing and taxes calculations, availability checks, initial documents generation (Specifications, Consignments, Invoices, etc.)
- Intercompany: Initial documents auto-generation for related Company Codes (background mirror documents forming)
- Sales Planning in a single SAP S/4HANA system
PP — production planning
- Master data management — material masters clearance, BOM and Recipes created and enriched for all products
- Actual stock balance of materials in on-line mode
- Real-time radars/flowmeters/weighbridge integration with auto-postings to SAP (SCADA-SAP integration)
- Production cockpit — online production confirmation by operators
- Long term and operative production planning based on sales plans
- Material requirements planning (MRP) based on the production plan based on the sales plan
- Automatic production costing
QM — quality management
- Total quality control at all production stages:
- Purchasing/transportation/registration/storage/production/sale of finished goods
- Materials batch traceability
- Forming of required reporting
- Certificate management system: Quality Certificates printing eliminating the possibility of manual changes
- Online quality control in a single system for both plants: Palm and Crush (before implementation Palm Plant operations were not managed in any accounting system)
- Surveyor workplace in SAP: ensure QM online control in single S/4HANA system